10 Ways to Boost Employee Engagement in Manufacturing Companies
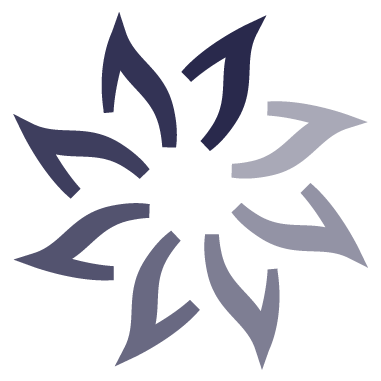
A Global Employee Recognition and Wellness Platform
A manufacturing setting is far from a typical office aesthetic environment. Most facilities operate twenty-four hours and beyond without a day off. Working conditions are unfavorable for employees, lacking a safe environment, excessive noise, stifling heat, and poorly lit spaces. All these contribute to a challenging workspace, further aggravated by long shifts and physically demanding work. As a result, the engagement levels drop, and the company faces high turnover.
-
According to a Manufacturing Industry Report, 62% of manufacturing organizations reported an increase in turnover year-over-year.
-
According to a PWC study only half (48%) of manufacturing leaders say that most of their frontline workers feel engaged in their jobs.
Statistics highlight the alarming and deteriorating consequences of the manufacturing industry. This is where strengthening employee engagement in manufacturing becomes crucial.
This blog will highlight the importance of employee engagement and discuss practical initiatives to improve engagement in the manufacturing industry. It will also highlight the challenges that need your attention, helping you take actionable steps to boost employee morale and reduce turnover.
Key Takeaways
- Why employee engagement matters in the manufacturing industry
- What are the challenges of employee engagement in the manufacturing sector
- How to improve employee engagement in manufacturing
- What are the ways to measure manufacturing employee engagement
Why Employee Engagement Matters in the Manufacturing Industry
Given the alarming statistics and scenario of the manufacturing industry, it’s clear that improving employee engagement is vital to helping the sector recover and thrive. The following reasons will further emphasize the importance of employee engagement in the manufacturing industry today.
Let’s dive into how engagement can drive your employees to deliver quality performance and stay committed to the company longer.
1. Increased Productivity and Efficiency
Productivity and efficiency are the heartbeats of the manufacturing industry. Engaged employees are vital to enhancing both. Employees who are emotionally invested in their work are willing to go the extra mile, whether staying focused during extended shifts, minimizing production bottlenecks, or constantly enhancing processes.
In a manufacturing environment, any form of delay or inefficiency can cause unwanted disruptions, costing the company its time and resources. However, engaged employees are less inclined to get distracted. Instead, they showcase their proactiveness through streamlining operations, optimizing workflows, and finding solutions to challenges that could otherwise impact output.
2. Improved Quality Control
Quality control is a non-negotiable aspect of manufacturing, and engaged employees are critical to maintaining it. They do not just follow the production line; they are invested in the final product. They are willing to undertake ownership of their work, ensuring that every product stands aligned with the company standards. Being engaged enables them to proactively indulge, spot potential issues, catch defects, and take extra care with the production process.
This sense of responsibility infused in them, driven by engagement, leads to fewer errors and rework, which is otherwise time-consuming and costly. Emotional connection pushes them to maintain high standards, improve consistency, and enhance the company’s reputation for quality.
3. Reduced Turnover and Absenteeism
One of the biggest challenges that continues to haunt the manufacturing industry is employee turnover. The physical nature of the work, long-hour shifts, and job monotony largely contribute to subsequent high turnover rates and absenteeism. This is mainly because they feel disconnected from the company, which is a defining factor in increasing disengagement. As a result, they seek better opportunities elsewhere.
On the contrary, engaged employees are more likely to stay with the company for the long term. Engaged employees willingly commit to the company’s mission and develop a sense of camaraderie with their team. As a whole, it contributes to improving morale and reducing turnover and absenteeism.
4. Customer Experience
Engaged employees do more than simply manufacture better products and upgrade their productivity levels; they actively provide better customer service. Exceptional customer service is directly linked to repeat customers and business.
By keeping your employees engaged, you ensure they deliver the best possible customer experience in return.
As per a Gallup study, companies with engaged employees showcase 10% higher customer loyalty/engagement. They take personal ownership of making customers happy and are willing to go the extra mile.
Recommended Resource: How Employee Satisfaction Can Lead to Customer Satisfaction
Challenges of Employee Engagement in the Manufacturing Sector
Employee engagement in the manufacturing industry comes with its set of challenges. Having been associated with long hours, physically demanding work, and a high turnover rate, keeping employees engaged is challenging. These conditions often lead to disengagement, impacting their morale and productivity.
However, you can counter these challenges by recognizing them and addressing them through solutions to overcome them. So, let us explore the challenges and their respective solutions.
1. Repetitive Tasks and Monotony
The nature of repetitive tasks is one of the daunting challenges in manufacturing. Employees end up performing the same set of duties regularly. This repetition further seeps into monotony, where workers feel their efforts are undervalued, leading to disengagement. The lack of variety and experimentation can be mentally and physically draining, dropping motivation and job satisfaction levels.
To counteract the monotonous cycle, manufacturers can develop strategies like job rotation or cross-training. Allowing employees to periodically move between different roles and departments will help them gain new skills, stay engaged, and put an end to the burnout resulting from repetitive tasks.
Incorporating variety in their daily work can boost employees’ motivation and motivate them to tackle new challenges. This will help them acquire and master the latest skill sets for the new business area.
2. Lack of Communication and Recognition
In the manufacturing industry, the emphasis on production targets, deadlines, and efficiency often overshadows communication and employee recognition. Employees may feel that their efforts go unnoticed, leading to a sense of frustration and isolation. With the lack of communication, employees find it challenging to grasp the company’s vision, understand how their role fits in the big picture, and know where they stand in terms of their performance.
To counteract these issues, leaders in manufacturing must prioritize and practice regular feedback and establish employee recognition programs. Providing frequent and constructive feedback helps employees understand their strengths and areas for improvement. Ensuring two-way communication through regular meetings and check-ins ensures that employees feel heard, valued, and involved in decision-making.
Additionally, recognition programs conferred through awards, shoutouts, or team celebrations validate their efforts. This goes a long way in boosting morale and engagement.
3. Limited Growth Opportunities
One of the root causes of disengagement in manufacturing is the perception of limited career advancement. The roles assigned to employees in this sector seem more like dead-ends, leaving little to no room for growth. As a result, employees who are eager to expand their careers get demotivated. When employees feel that there are no opportunities to move up or acquire new skills, they may lose their purpose and commitment to their roles.
To counteract this, manufacturers must emphasize providing career and skill development programs along with mentorship opportunities. This will enable the employees to enhance their learning curve and ensure growth. Mentorship opportunities provide employees with a mentor or career coach that helps them visualize their potential career trajectory. These initiatives show employees that the company is dedicated to their long-term growth, which ultimately increases engagement and reduces turnover.
How to Improve Employee Engagement in Manufacturing
The lack of employee engagement haunting the manufacturing industry continues to be a pressing issue that requires serious attention from the leaders. This is where the need to engage the employees arises, which can be achieved by implementing activities and ideas.
Let’s take a closer look at some employee engagement ideas for the manufacturing sector.
1. Paid Lunches or Snacks
Nothing can be more rewarding than a meal for a hardworking front-line employee. In a factory setting, offering occasional paid lunches through food trucks or catering is one simple yet effective way to boost employee engagement.
Complimentary lunches and snacks encourage rapport-building among team employees in a relaxed setting. This is beyond the requirement of free meals for employees; for them, it’s a gesture signifying how their leaders acknowledge their hard work and value their well-being. The break hours assigned for lunch or snacks can enhance productivity and contribute to a positive workplace culture.
2. Safe Work Environment
Ensuring a safe work environment should be a priority for the leaders of any organization. However, this is often compromised, particularly in the manufacturing industry.
Until and unless employees feel safe at work, they cannot deliver work to their best abilities, distancing them from getting engaged.
Hence, prioritizing workplace safety helps employees get engaged. In turn, these employees will strive to improve safety moving forward.
A Gallup research shows that engaged workplace environments have 70% fewer safety incidents.
Managers and leaders must take the lead in regularly assessing the safety performance of equipment and protective wear. They should undertake proper risk assessment and ensure safety protocols are in place before the employees are put to work. This helps prevent future risks.
However, physical safety is not the only safety employees seek; it is equally important to foster a company culture that ensures psychological safety. This safety enables employees to voice their opinions without worrying about being judged or punished.
Once their physical and psychological safety is taken care of and employees leave their worries behind, they-
- Feel a greater sense of morale
- Feel valued and supported
- Focus on higher productivity and quality delivery
- Develop trust in leadership
3. Recognize Employees
Every employee deserves to be recognized for the hard work they put in. And this particularly applies to the employees in the manufacturing company, who are facing heavy disengagement and turnover. Recognition can be one significant aspect that can help leaders and managers pull their industry from the troubling scenario.
According to a Manufacturing Institute Report, employees who feel valued were more than four times as likely to report high levels of work engagement.
The value that employees seek is attained when they get validation for their hard work and achievement through recognition. Celebrating the small and big wins adds to the feeling of value and increases their morale.
If you are pondering how to appreciate and celebrate workers, it is best to know how the employees wish to be acknowledged. Managers should directly ask the employees about their preference for appreciation, whether privately, publicly, peer-to-peer, manager-to-employee, or a mix of everything. Accordingly, you can plan the recognition programs and build a culture of regular recognition, emphasizing the significance of instant recognition.
A Gallup study shows that employees who strongly agree that their manager holds them accountable for their performance are 2.5 times more likely to be engaged in their jobs.
4. Performance-based Incentives
Although incentives may not be the ultimate factor of employee engagement, they are nonetheless crucial. Offering performance-based incentives is a rather significant employee engagement idea in manufacturing.
Monetary incentives that you can consider cover team bonuses, profit-sharing schemes, and bonus programs against meeting production targets. The very idea of getting rewarded for showcasing worthy performance will ignite them to work efficiently and enhance the quality simultaneously.
5. Consider Flexible Scheduling
While flexible scheduling may not always be a plausible option for many employees, leaders should nonetheless look for ways to make work-life hassle-free for workers. If you can provide flexibility through staggered shifts or task-based schedules, you can grab the opportunity to earn the trust and loyalty of your employees. This effort from leaders will motivate the employees and enhance their productivity during work hours.
Recommended Resource: Flexible Working Hours: 5 Ways It Boosts Productivity
6. Prioritize your Onboarding Experience
The initial stage of onboarding the employees into your organization is crucial for setting the tone for employee engagement. Ensure that you make the best of this opportunity by making this experience pleasant and memorable for the employees.
Train new joinees in a way that allows them to get clarity about their roles. Also, provide necessary information on where the company is headed, how the employees fit in the larger picture, what are the available resources, perks and benefits, etc.
7. Develop Open Lines of Communication
Two-way communication is one of the crucial steps to employee engagement. Managers and leaders should transparently communicate the big and small decisions about the company and the reasons behind it. Also, highlight and explain the connection of how their work contributes to the company goals. This builds trust among employees, allowing them to understand the significant positioning of the company.
Also, ensure employees get the liberty to voice their ideas and concerns about the company or leadership. Listening to what they have to say makes them feel heard, understood, and valued, which, in turn, are crucial factors to get them engaged.
8. Pay Employees Fairly
The highest number of complaints that manufacturing workers associate with their work is unfair pay. Compensation may not be everything. However, if you choose not to pay your employees fairly or don’t give justification as to why they are paying the way they are, it is highly likely for them to not commit to you in the long run.
9. Offering Career Growth Opportunities
No employee desires to remain stagnant in their career path. Everyone is on the lookout to upgrade their skill sets. One of the key ways to keep your employees engaged is to offer them upskilling opportunities and fill in the skill gaps many fall into. This will allow them to explore the endless possibilities of enhancing their capabilities and becoming an expert in their work.
Every worker may not find a traditional way to climb the career ladder, but you can help workers learn new skills and ways of operating in many ways you can.
A McKinsey Report shows that career development and advancement opportunities rank equally with compensation as the top factors determining whether people accept, stay in, or leave a job.
10. Foster Meaningful Relationships Across Teams
Engagement for frontline workers is more than just feeling connected to their work or company; it is also about making employees feel connected with their peers. It is about providing opportunities to employees that allow them to connect beyond their work environment, such as special events, team lunches, or team-building activities. These initiatives boost collaboration, encourage interpersonal relationships, and infuse a sense of community among employees.
Ways to Measure Manufacturing Employee Engagement
Now that you have explored potential ideas and activities to keep your employees engaged, how can the leaders determine that your engagement practices are genuinely effective.
This is where gauging the effects of employee engagement becomes crucial. Here are some ways to measure employee engagement in manufacturing.
1. Conducting Employee Surveys
Conducting employee surveys helps you derive input about what your employees feel about the job role and the opportunities given to them. Employee surveys come in different forms, from pulse surveys to Employee Net Promoter Score. However, managers should be vigilant that these surveys remain anonymous, which can make employees comfortable to give candid and genuine responses.
2. Hosting Regular One-on-Ones
Managers should have regular one-on-one meetings with the employees and derive a first-hand opinion from them about what they are finding well, where there is room for improvement, and how engaged they feel.
Managers should take a genuine interest in understanding the favorable and pain points and determine the follow-up actions they might need to take to address any alarming issues. In addition to understanding the engagement levels and potential problems, the one-on-one meetings allow workers to share their professional development goals.
3. Tracking Metrics
Apart from seeking feedback from frontline workers, leaders should also practice monitoring a range of metrics to gauge the efficiency of engagement efforts over time.
Some critical metrics that leaders need to keep track of are turnover rates, retention rates, absenteeism rates, and productivity levels. These metrics will provide concrete data to understand how well your engagement efforts have fared for you.
Conclusion
Having explored the importance, challenges, and ideas to improve employee engagement, it’s time for the manufacturing industry to implement the necessary changes to allow its employees to thrive.
As leaders, you can create a thriving workplace where your employees can envision a future of growth and expand their productivity.
FAQs
How can manufacturing companies ensure their employee engagement efforts are sustainable?
Sustainability in engagement efforts can be achieved by:
- Creating long-term plans: Develop continuous engagement strategies that evolve with the needs of the workforce.
- Involving employees in decision-making: Empower employees by involving them in decision-making processes, especially in areas that affect their work.
- Monitoring and adjusting programs: Regularly assess engagement programs and make adjustments based on feedback and performance metrics.
What role does leadership training play in employee engagement in manufacturing companies?
Leadership training is vital in fostering employee engagement. Leaders who are well-trained in effective communication, conflict resolution, motivation, and employee recognition are more likely to build strong relationships with their teams and create an engaging work environment. Leadership development programs can help managers better support their teams, ultimately improving engagement and performance.